Flame Straightening
Bill Casper introduced this remarkable repair method to the crane industry in 1982 after attending a Saturday seminar by Professor Richard E. Holt, University of Washington metallurgical engineer.
Professor Holt’s father, Joe Holt, was a Seattle blacksmith who invented the repair applications for this process. In 1938 Joe authored a technical paper with a description and examples of flame straightening applications. It remained more art than science until his professor son came up with an engineer’s explanation for why and how the system worked and could be controlled.
Today the process is termed “Thermal Upsetting” and is recognized by AISC, AASHTO, and AWS. Flame straightening is also commonly referred to as heat straightening. Heat straightening is not limited to repairs. The impressive Seattle Space Needle could not have been built with the double curvature legs without the use of flame bending. Navy shipyards routinely use this process to pre‑shape continuous piping so it can be welded together without forcing parts together for welding.
CP&A has worked for many years with Holt relatives and other specialists who were trained by the Holt family. This has been a two‑way learning and growing process where CP&A has gained practical application experience to complement our analytical engineering talents. The field experts have gained a better and better understanding of why the process works and how it can be accomplished more efficiently.

Bridge girder was plastically deformed. Successful repair using flame straightening or thermal upsetting.

STS container crane boom suffered thin panel buckling on boom. Successful repair by flame straightening.
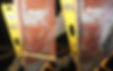
A structural bridge member was damaged. heat straightening.

Bridge girder was plastically deformed. Successful repair using flame straightening or thermal upsetting.
Flame Straightening FAQ
Q: How does flame straightening work? A: Consider a short steel bar placed snug tight in a highly rigid vise. In this condition it is unstressed except for residual stress that may have been introduced when the bar was rolled or cold worked. Now gently heat the bar with a torch. As heat is added the steel volume increases and yield stress decreases. Longitudinal expansion is prevented by the vise but the bar is free to expand in width and thickness. For ordinary structural steel 200° F is enough for compression stress to reach the slightly reduced yield stress in the restrained direction. Any further thermal expansion is permanent post yield distortion and occurs in the two unrestrained directions. Common field practice for ordinary structural steel is to heat to 1,200° F. The higher temperature further reduces yield strength and, by thermal expansion, further increases the steel volume in the two unrestrained directions. Now allow the bar to air cool. As it cools it changes all three dimensions by the usual rules for thermal contraction. After cooling, the net result, including the previous plastic volume increase in the two unrestrained directions, produces a wider and thicker but shorter steel bar. The bar may actually fall free of the vise. The bar is once again free of all stress other than new residual stresses that are usually much less than the residual stresses that were present before the first heat. This process is repeatable over and over again if the vise is first made snug tight. Each heat cycle will produce measurable dimensional changes. Residual stresses existing at the beginning are removed and replaced with new cooling residual stresses that remain about the same cycle after cycle. In a real structure there is no vise and thickness is the only unrestrained dimension. Thus the term “Thermal Upset”. The surrounding unheated steel serves the same purpose as the vise described above. The heat is applied by slowly moving a hot spot along a specific path to cover a specific heat-treated shape that will produce a particular desired effect. For example, a triangular shape can be pictured as a series of bars side by-side that start at a single spot and increase in length with each pass of the torch so the total zone has a triangular shape. The net effect after cooling is that a longer pseudo bar shortens more than the adjacent shorter pseudo bar. This thermally bends the structural member without ever heating to a metallurgical high temperature or any need to mechanically bend heat softened steel. The heating cycles can be repeated with each cycle moving the member closer and closer to the desired end result. It can be used to intentionally camber a beam or to straighten a beam that has been accidentally bent.
Q: Is this process damaging to the structure’s metallurgical properties? A: Absolutely not. For heat hardened steels such as A514 the proper temperature will usually be less than 1,200° F; say 800°F or 900°F, so the hardening is not lost. There has been no metallurgical change except possible beneficial normalizing as the steel air cools. This normalizing effect has been implied on some bridge repairs because the Charpy toughness increased at the heated zones. Any steel that can be welded can be flame straightened. Consider what happens when steel is welded. The steel is melted to a liquid state. That may change the metallurgy of the heat affected zone and then cooling shrinkage can add shrinkage stress that usually reaches yield stress where it can continue to shrink at full yield stress. By comparison, flame bending is an extremely gentle process. Also consider that steel fabricators routinely use this basic process every day to correct weld distortions and camber members. The only difference is that shop workers are trained to perform a specific task without need to understand or care why the process works. A skilled flame straightening technician needs basic knowledge because each repair project has unique challenges that may or may not be similar to previous projects.
Q: What about dead load stresses that still exist in an accidentally damaged structure? A: This is a factor that must be evaluated but is seldom a concern for an experienced flame straightening technician. At any instant during the heating process only an individual small spot is being heated to 1,200° F. The surrounding steel that is in direct contact with that spot is already cooling or is gaining heat as the torch moves toward it. Usually the zone of softer steel is so small in proportion to the much larger structure that the loss of dead load strength is insignificant. Bent compression members may need external restraint to avoid further compression bending.
Q: The process is labor intensive and experienced technicians have high hourly rates. Can the work be speeded up to save cost? A: Yes. The best way to speed the process can be demonstrated with the bar and vise. Instead of starting snug tight, experiment with a tighter and tighter vise. Pre-compression is a very effective method to get more upsetting per cycle. For a real structure the pre compression restraint comes from hydraulic jacks or various types of pulling gear. Often, devising an effective restraint scheme is an engineering challenge. One good rule is to apply a restraining force in the opposite direction to the accidental load that caused the original damage. This is very effective if the rigging situation makes this practical to do.
Q: What are the most important precautions when flame straightening? A: For the answer, go back to the basics that are best demonstrated by the bar and vise. Consider what happens when the bar length is too long in proportion to the bar thickness or width. Pre-compression or heating compression against the vise can cause local buckling of the bar. For a real structure the proper precaution is to keep the length to thickness ratio small enough to avoid local buckling. There is no hard rule because each situation is different. This is why specialists are worth their high hourly rates. Once local buckling occurs it is not easy to erase the damage. Another important precaution is to be aware of the danger of tension type restraints suddenly failing. As heat is being applied, the tension force may dramatically increase so that a safe initial tension grows to a failure tension. A final cautionary note is to be patient. The process works best when it can proceed to conclusion without mishaps or need to reverse a previous heat. This is especially true when the straightening nears completion and the task is to anticipate how much pre-compression and heat it takes to end near zero tolerance without going to far the other way after the member cools. Over-shooting at this point can require re-rigging to reverse the straightening direction.
Q: Why not simply cut out bent members and install new members? A: The repair cost ratio for replacement vs. flame straightening is often 2 or more favoring flame straightening. Sometimes it is 10, 20, or even more times cheaper. An equally important reason is that flame straightening restores pre accident geometry unless members have been torn or deliberately cut out of the damaged structure before the flame straightening is started. Replacement probably will not restore original geometry unless the undamaged geometry was well documented prior to the accident. Original shop drawings are helpful but they may or may not be an accurate record of pre accident geometry.
Q: How or why does flame straightening restore pre accident geometry? A: Wherever the accident permanently bent members, these members remain with residual elastic stresses at full yield level. These residual stresses, tension and compression, are all trying to restore the original shape. This effect can be favorably amplified when it is possible to apply a restraining force in the opposite direction and at the location where the load that caused the damage was applied. An experienced technician uses these residual stresses to assist the repair. That is done by applying straightening techniques that allow the residual stresses to relax to near zero without forcing new residual stresses elsewhere. If this action is also being assisted by favorable restraints then the complete repair can be completed by allowing the structure to go where it wants to go. Additional flame straightening can be used to force the structure back to original shape, or to another shape that is fully acceptable to the owner. Either way, individual members have retained their pre accident length.
Q: Is flame straightening the same thing as heat straightening? A: Yes, flame straightening and heat straightening can be used interchangeably.
Q: Is flame straightening the same thing as hot rolling? A: No, they are completely different processes. For hot bending and hot rolling, the entire piece of steel is heated up to around 1,700°F (925°C) depending on the grade of steel. The primary shaping mechanism is the external forces. Flame straightening only heats up a small area and uses much lower temperatures. For example, the maximum thermal upsetting temperature for A572 is 1,100°F. The basic mechanism of heat straightening is to create plastic flow through applying heat in specific patterns to gradually straighten the steel. External force is not the primary mechanism of straightening. Using thermal expansion as the primary mechanism helps maintain the material properties.